The heat treatment process has applications to alter the material’s mechanical properties. The type of heat-treatment process determines what will change in material mechanical properties. This article covers various types of heat treatment processes with examples.
What is Heat Treatment Process ?
The Heat Treatment process involves the heating and cooling of materials to change their physical and mechanical properties. Heat Treatment in metal parts has the following applications.
- Increase hardness, ductility, strength, formability, and machinability.
- Improve softness & corrosion resistance.
- Relieve internal stresses.
Benefits of Heat Treatment
The Heat Treatment process changes steel mechanical properties according to the requirements. It has the following advantages:
- Can Increase the hardness of material on surfaces only.
- Remove internal stresses.
- Increase product life.
- Improve weldability.
- Improves material dimensional stability, toughness and reduces hardness by relieving stress.
Heat Treatment Techniques
- Hardening
- Annealing
- Tempering
- Normalizing
- Case or Surface Hardening
- Case Carburizing
- Cyaniding
- Nitriding
- Flame Hardening
We will discuss all of the above heat treatment techniques in detail.
1. Hardening
During the hardening process, the material is heated above its normalization temperature and kept there for the required time. After heating, quenching (cooled it rapidly) of material in water or oil. Hardening of steel:
- Improve Strength.
- Increase Hardness.
- Improve toughness and elasticity.

The material heats up throughout its thickness during the heating process. As a result, the complete material structure converts to austenite. The tempering process after Hardening improves part dimensional stability and toughness.
2. Tempering
The Tempering heat treatment process involves reheating martensitic steel below its critical temperature ( or eutectoid temperature ) and afterward cooling it slowly.
Hardened or normalized steel tempering operation improves material dimensional stability, toughness and reduces hardness by relieving stress produced during quenching. The actual tempering temperature depends on the required properties of a material.
If the tempering temperature is high, material Ductility will increase. But the strength and hardness reduce. Therefore by changing the tempering temperature, we can modify material properties.
3. Annealing
The Annealing heat treatment process involves heating the material 20ºC above its critical temperature, soaking it at the same temperature for 1 to 2 hours, and then cooling it slowly at room temperature.
The material is cooled slowly to release internal stresses and re-arrange ferrite and pearlite structures during the annealing process.
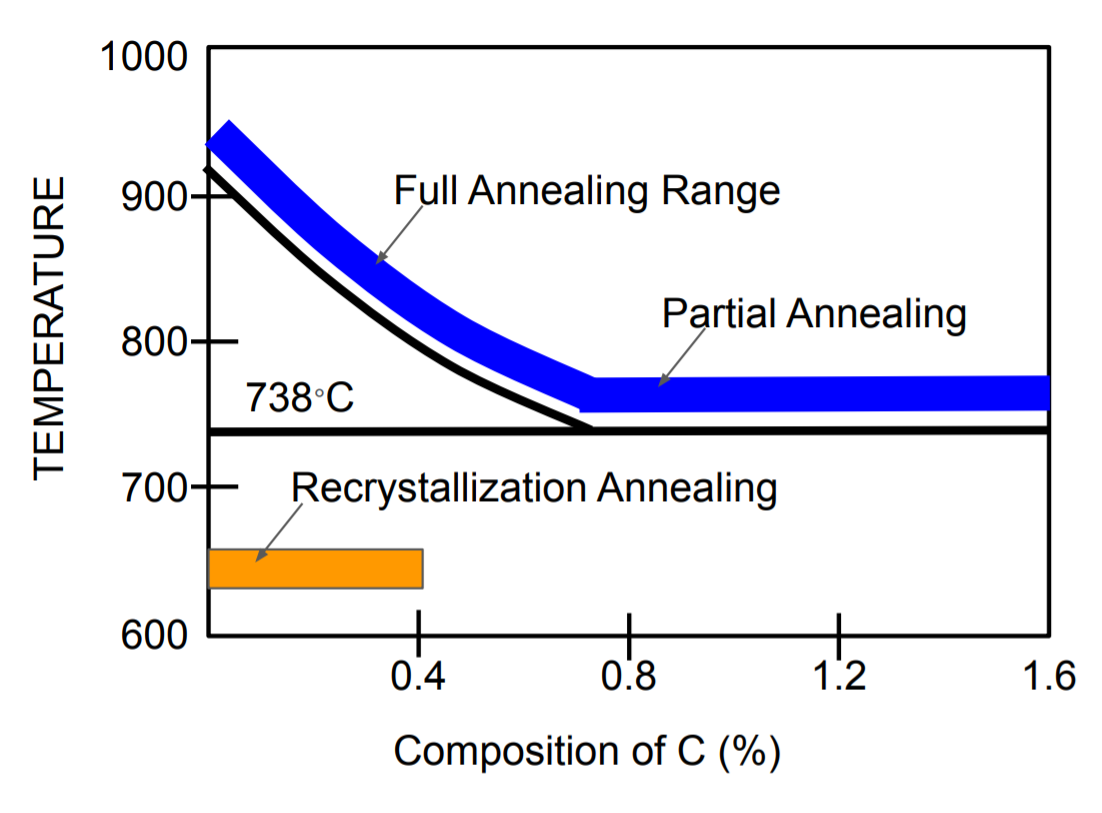
Annealing is generally used for ferrous and non-ferrous materials to reduce Material hardness before or after the cold working operation. It has the following applications.
- Refine the microstructure of the material.
- Remove internal stresses.
- Improve machinability, ductility, and toughness of the material.
- Reduces hardness
- Remove gaseous contents from steel.
4. Normalizing
During the normalizing heat treatment process, steel is heated at 40º to 50º above the upper critical temperature, holding it for 10 to 15 minutes and cooling in the open air. As a result, the material grain size becomes uniform.
Normalizing is done on carbon steels to:
- Improve material strength.
- Ductility reduces.
- Eliminate internal stresses.
- Restructure material grains.
The case or surface hardening process hardens the outer surface to resist wear and erosion. In case-hardening, the material inner surface remains soft and tough to handle impact load.
For example, the case hardening process has application to harden tool and die outer surfaces only. Following types of case hardening processes are available in the market.
- Case Carburizing
- Cyaniding
- Nitriding
- Flame Hardening
5.1) Case Carburization
Case carburization process involves heating the steel below the melting point in the presence of high carbon material such as charcoal.
As the result of carburization, the material hardness increases because the outer surface absorbs the carbon. Depth of carburization depends on the time of carburization and temperature.
5.2) Cyaniding
Cyaniding involves immersion of material in the bath of sodium chloride, sodium carbonate, and sodium cyanide at around 900ºC and then quenching in cold water or oil. It has the advantage of uniform hardness and a good surface finish.
5.3) Nitriding
Nitriding involves heating of steel above 500ºC in the presence of ammonia. It results in the formation of nitrides on the surface that is hard.
5.4) Flame Hardening
The Flame hardening process involves heating the surface to be hardened using oxyacetylene flame up to the required temperature and then quenching it in water or oil. This process has the advantage of the possibility of localized hardening.
We will keep adding more information on the heat treatment process to alter the mechanical properties of steel. Add your comments, suggestions, or questions on heat treatment processes in the comment box.
Add a Comment